Toroidal field (TF) coils
Topology of TF coils and Central Solenoid
The engineering models are based on a topology like that used in ITER: the central solenoid and the TF coils are not linked: the central solenoid can be inserted or removed without cutting the TF coils.
However, an option does exist wich permits the alternative topology, in which the inboard legs of the TF coils pass through the middle of the central solenoid. This layout is used in MAST, where the copper TF coils can be dismantled to allow the central solenoid to be inserted or removed.
The topology is set as follows:
- tf_in_cs = 0
(default) ITER-like topology: the central solenoid and the TF coils are not linked.
- tf_in_cs = 1
The inboard legs of the TF coils pass through the middle of the central solenoid. Note that this model does not provide a physically self-consistent result for superconducting coils.
Coil type
Two major types of toroidal field (TF) coils can be considered in PROCESS: Resistive magnets or Superconducting magnets. The choice of conductor type is made using the following integer switch:
i_tf_sup == 0
: Resistive copper or copper alloy magnets with water cooling.i_tf_sup == 1
: Superconducting magnets with helium cooling.i_tf_sup == 2
: Resistive aluminium (high purity) magnet with helium cooling at low temperature (15-30 K at the helium inlet).
This section presents the PROCESS TF coil models and how to use them. The associated module computes first the coil current from the plasma major radius and toroidal magnetic field. The inboard leg mid-plane cross-section geometry is then set up to the conductor level. The vertical geometry is defined and the TF components masses are deduced. The inboard mid-plane stress distributions, the coil inductance and the toroidal field ripple are then estimated. Finally, the resistive heating (if resistive coil) and the ratio between the critical current density and the conductor current density (superconducting coil) is estimated.
TF coil currents
The total current flowing in the TF coil set I_\mathrm{TF}^\mathrm{tot} (ritfc
) is calculated using the approximation of axisymmetry from the vacuum toroidal field at the plasma geometric centre B_\mathrm{T} (bt
) and the plasma geometric major radius $ R_0 $ (rmajor
):
This approximation is sufficiently accurate at the plasma centre.
TF coil inboard mid-plane geometry
This section describes TF coil inboard leg geometry of the cross-section defined by z=0 (mid-plane). Resistive and superconducting coils are described separately.
Superconducting coil geometry
The TF coils are assumed to be supporting each other against the net centering force. This can be described as a vaulted or wedged design. Each coil, illustrated in Figure 1, can be separated in two main sections:
- The winding pack (WP) : section containing the superconducting cables (Blue area in Figure 1). The ground insulation and the insertion gap (the clearance required to allow the winding pack to be inserted, shown as the dark grey area in Figure 1) is considered part of the WP by convention.
- The steel casing: Section holding the WP providing the necessary structural support (light grey area in Figure 1).
The next sub-section describes the different parametrization proposed in PROCESS:
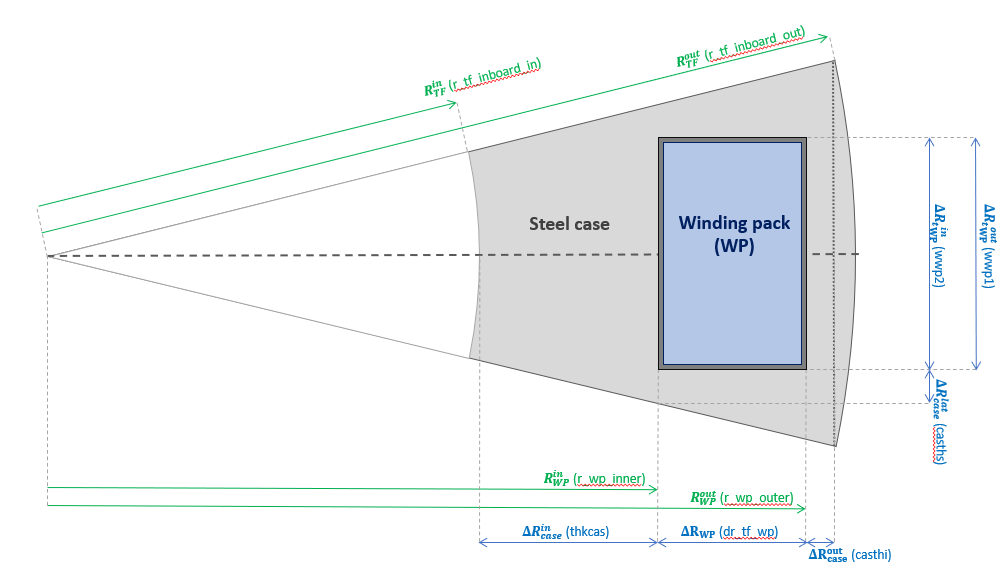
Figure 1: Inboard mid-plane cross-section of the superconducting TF coils considered in PROCESS with associated parametrization. The green variables are calculated by the machine_build module subroutine while the blue ones are specific to the sctfcoil module. The light grey area corresponds to the steel casing containing the Winding pack and providing structural support. The dark grey area corresponds to the winding pack insertion gap, and its ground insulation. Finally the light blue area corresponds to the winding pack containing the conductor cables. More details on the parametrization is discussed in this section.
TF coil inboard radial size
Following the geometry and its parametrization presented in Figure 1, the TF total thickness tfcth \( \left( \Delta R_\mathrm{TF} \right) \) is related with the inner and outer case radial thicknesses (thkcas, \( \Delta R_\mathrm{case}^\mathrm{in} \) and casthi, \( \Delta R_\mathrm{case}^\mathrm{out} \) respectively) and the WP radial thickness dr_tf_wp \(\Delta R_\mathrm{WP}\) by the following equation :
with \( R_\mathrm{TF}^\mathrm{in} \) (r_tf_inboard_in) the radius of the innermost TF edge, set by the central solenoid coil size and \( N_\mathrm{TF} \) the number of TF coils. Reverted, to provide the WP thickness, the same equation simply becomes:
The TF coil radial thickness (tfcth) can parametrized in two ways in PROCESS:
Direct parametrization: the TF radial inboard thickness width is set as an input variable :
tfcth
(iteration variable 57). The WP radial thickness (dr_tf_wp
) is calculated fromtfcth
and the two case radial thicknesses. This parametrization is used by default.WP thickness parametrization: the TF inboard radial thickness is calculated from the the case and the WP radial thickness. This option is selected by using the WP thickness (
dr_tf_wp
, iteration variable 140) as an iteration variable. Doing so, anytfcth
values will be overwritten and for this reasondr_tf_wp
andtfcth
cannot be used as iteration variables simultaneously. Although not set by default for backward compatibility, this parametrization provides a more stable optimization procedure (negative WP area layer cannot be obtained by construction) and is hence encouraged.
Case geometry
Although not physically divided into pieces, three sections of the case can be considered:
The nose casing: this section corresponds to the case separating the WP with the machine center. Due to the presence of net electromechanical centering forces, this case has a major structural purpose and is often much larger than the other sides. The nose case dimension is set by its radial thickness that the user can specify using the
thkcas
input variable (iteration variable 57).Sidewall casing: this section corresponds to the lateral side of the case, separating the WP with the other vaulted coils. As in the WP geometry is generally squared, the sidewall case thickness may vary with the machine radius. For this reason, the user sets its dimensions though its minimal thickness
casths
. The user can either directly specifycasths
or define it as a fraction of the total coil thickness at the inner radius of the WP (r_wp_inner
) with thecasths_fraction
input. Ifcasths_fraction
is set in the input file, thecasths
value will be overwritten.Plasma side casing: this section corresponds to the case section separating the WP with the plasma. As the geometry of this section is rounded, its thickness is set by its minimal value
casthi
(user input). This parameter can also be defined as a fraction of the total TF coil thicknesstfcth
usingcasthi_fraction
. If thecasthi_fraction
parametrization is used, thecasthi
value will be overwritten.
Two different plasma side casing shapes can be selected using the i_tf_case_geom
integer switch:
i_tf_case_geom = 0
: The case has a rounded (cylindrical) profile on the plasma side. As it is the ITER design choice, this configuration is taken as default.i_tf_case_geom = 1
: The case has a flat profile on the plasma side.
Figure 2 illustrates the two plasma side casing configurations.
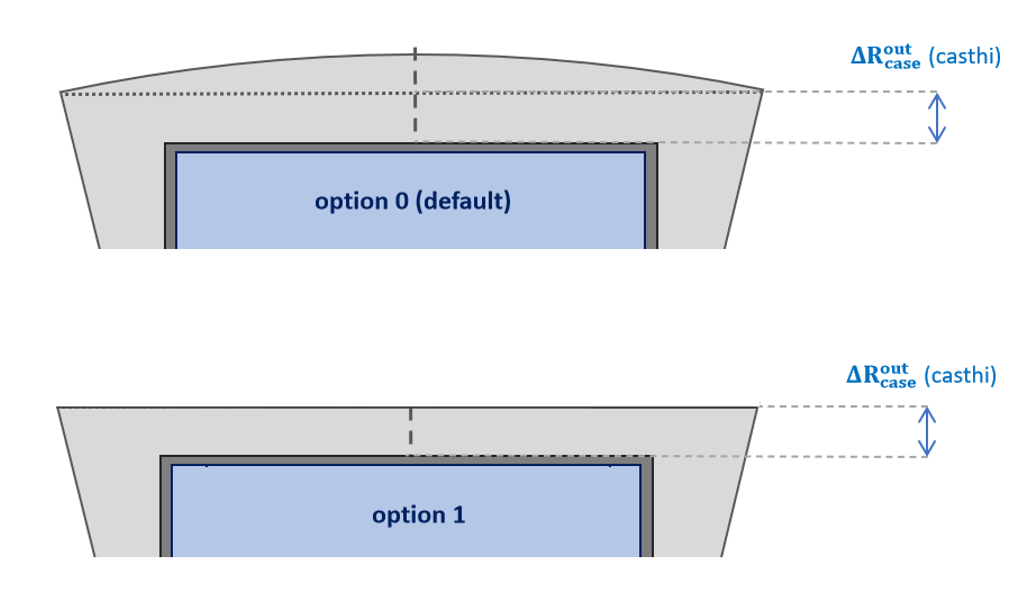
Figure 2: Visual illustration of the two front casing geometry options. The to diagram shows the default i_tf_case_geom = 0 rounded option and the bottom the i_tf_case_geom = 1 straight option.
Winding pack geometry
Several Winding pack geometries can chosen with the i_tf_wp_geom
integer switch as shown in Figure 3:
i_tf_wp_geom = 0
: Rectangular winding pack. It is the only geometry compatible with the integer turn parametrization (i_tf_turns_integer = 1
).i_tf_wp_geom = 1
: Double rectangle winding pack. The two rectangles are have the same radial thickness and their width in the toroidal direction is defined with the minimal sidewall thickness at their innermost radius.i_tf_wp_geom = 2
: Trapezoidal WP. The WP area is defined with a trapezoid, keeping the sidewall case thickness constant. This is however probably not a realistic shape as the turns are generally rectangular. This option has been added mostly to allow comparison with simplified FEA analysis configurations.
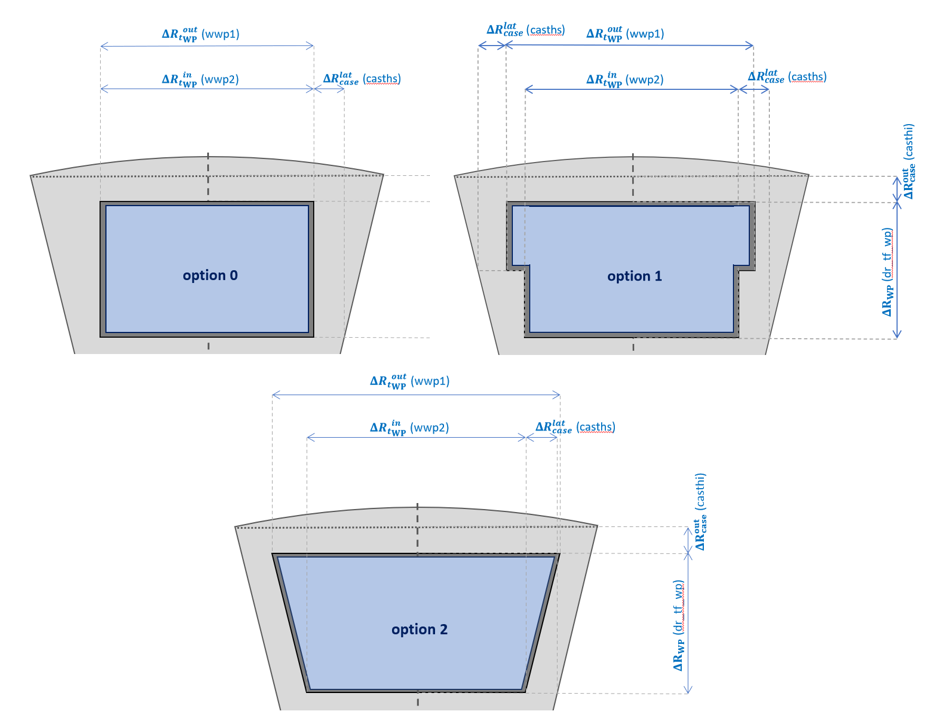
Figure 3: Visual illustration of the WP shapes the user can select with the i_tf_wp_geom integer switch. The wwp1 and wwp2 parameters, added in option i_tf_wp_geom = 1 are calculated using the minimal sidewall case thickness.
Turns geometry
Figure 4 illustrates the winding pack internal structure and the individual turns structure.
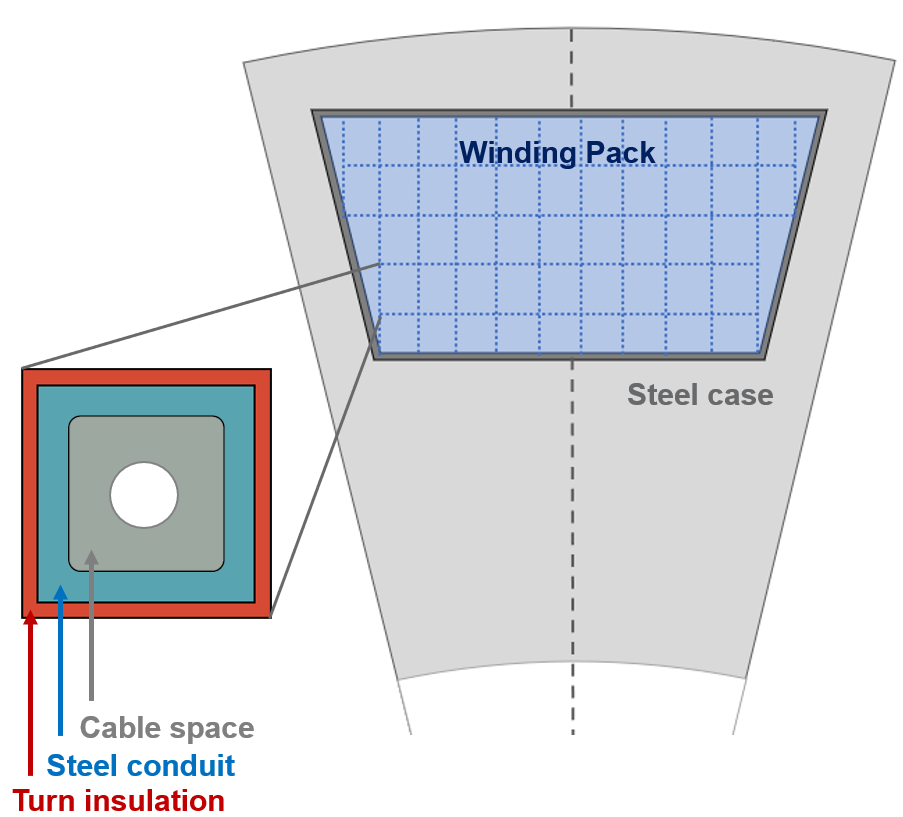
Figure 4: Illustration of the winding pack internal structure. The top right diagram shows the inboard mid-plane cross section of a TF coil with the steel case in light grey and the winding pack in light blue. The dotted lines illustrate the rectangular conductor. The bottom left zoom-in section shows the conductor structure used in the PROCESS module. The red section represent the individual turn electrical insulation, the turquoise the steel jacket/conduit providing structural support, the grey is the area allocated to the superconductor material, copper stabiliser and inter-strand coolant, and the white circle the helium cooling channel. (The superconductor, copper stabiliser and coolant together make up the 'cable'.)
The winding pack is assumed to be made of N_\mathrm{turn} (n_tf_turn
)
turns. The number of turns can be parametrized in three different ways :
Current per turn parametrization (default):
i_tf_turns_integer = 0
the user sets the value of the current flowing in each turnscpttf
. The number of turns necessary to carry the total TF coil current is then deduced fromcpttf
. There is no guarantee that a realistic turn configuration (with all the turn geometrically fitting in the allocated space) or even have an integer number of turn is used with this parametrization. If the turn thicknesst_turn_tf
or the cable thicknesst_cable_tf
is defined by the user, this parametrization is not selected.Turn size parametrization: the dimension of the turn
t_turn_tf
can be set by the user. To do so, the user just have to select the following option:i_tf_turns_integer = 0
and to set a value to the variablet_turn_tf
. The area of the corresponding squared turn and the number of turns necessary to fill the WP area is deduced. There is no guarantee that a realistic turn configuration (with all the turn geometrically fitting in the allocated space) or even have an integer number of turns is used with this parametrization. The current per turncpttf
will be overwitten.Cable size parametrization: the dimension of the SC cable
t_cable_tf
can be set by the user. To do so, the user just have to select the following option:i_tf_turns_integer = 0
and to set a value to the variablet_cable_tf
. The area of the corresponding squared turn is deduced adding the steel conduit structure and the turn insulation. The number of turns necessary to fill the WP area is then deduced. There is no guarantee that a realistic turn configuration (with all the turn geometrically fitting in the allocated space) or even have an integer number of turns is used with this parametrization. The current per turncpttf
will be overwitten.Integer turn parametrization:
i_tf_turns_integer = 1
the user sets the number of layers in the radial direction (n_layer
) and the number of turns in the toroidal direction (n_pancake
). The number of turns is integer. The turn cross-section is not necessarily square, giving different averaged structural properties in the radial and toroidal directions. Only a rectangular WP can be used for this parametrization.
The turn internal structure, illustrated in Figure 4, is inspired from the cable-in-conduit-conductor (CICC) design, with the main different being that a rounded squared cable space is used (grey area in Figure 4 ). The rounding curve radius is take as 0.75 of the steel conduit thickness. The turn geometry is set with with the following thicknesses:
Turn insulation thickness
thicndut
: user input setting the thickness of the inter-turn insulation.Steel jacket/conduit thickness
thwcndut
(iteration variable 58): user input thickness of the turn steel structures. As it is a crucial variable for the TF coil structural properties it is also an iteration variable.Helium cooling channel diameter
dhecoil
: user input defining the size of the cooling channel.
Cable composition
As the conductor cable composition is only used to correct the area used to compute current density flowing in the superconductor material, to be compared with its critical current density, an average material description is enough for the PROCESSmodels. The composition is set with the following material fractions:
Cable void fraction (
vftf
): user input setting the void fraction between the strands. This fraction does not include the helium cooling pipe at the cable center.Copper fraction (
fcutfsu
): user input setting the copper fraction. This fraction is applied after the void and helium cooling channels areas has been removed from the conductor area.
Resistive coil geometry
A much simpler inboard mid-plane geometry is used for resistive TF coils, as shown in Figure 6. The most important difference is the absence of the lateral steel casing structure. Three main sections can be distinguished:
- The bucking cylinder: radial thickness
thkcas
(iteration variable 57), is present to support the centering forces. Its presence is however not mandatory and can be can be removed setting TODO. - The conductor area: radial thickness
dr_tf_wp
(iteration variable 140). Ground insulation, corresponding to the dark grey area in Figure 6 is included in this section by convention. - The outer cylinder: radial thickness
casthi
. This cylinder plays no role in the structural models in PROCESS.
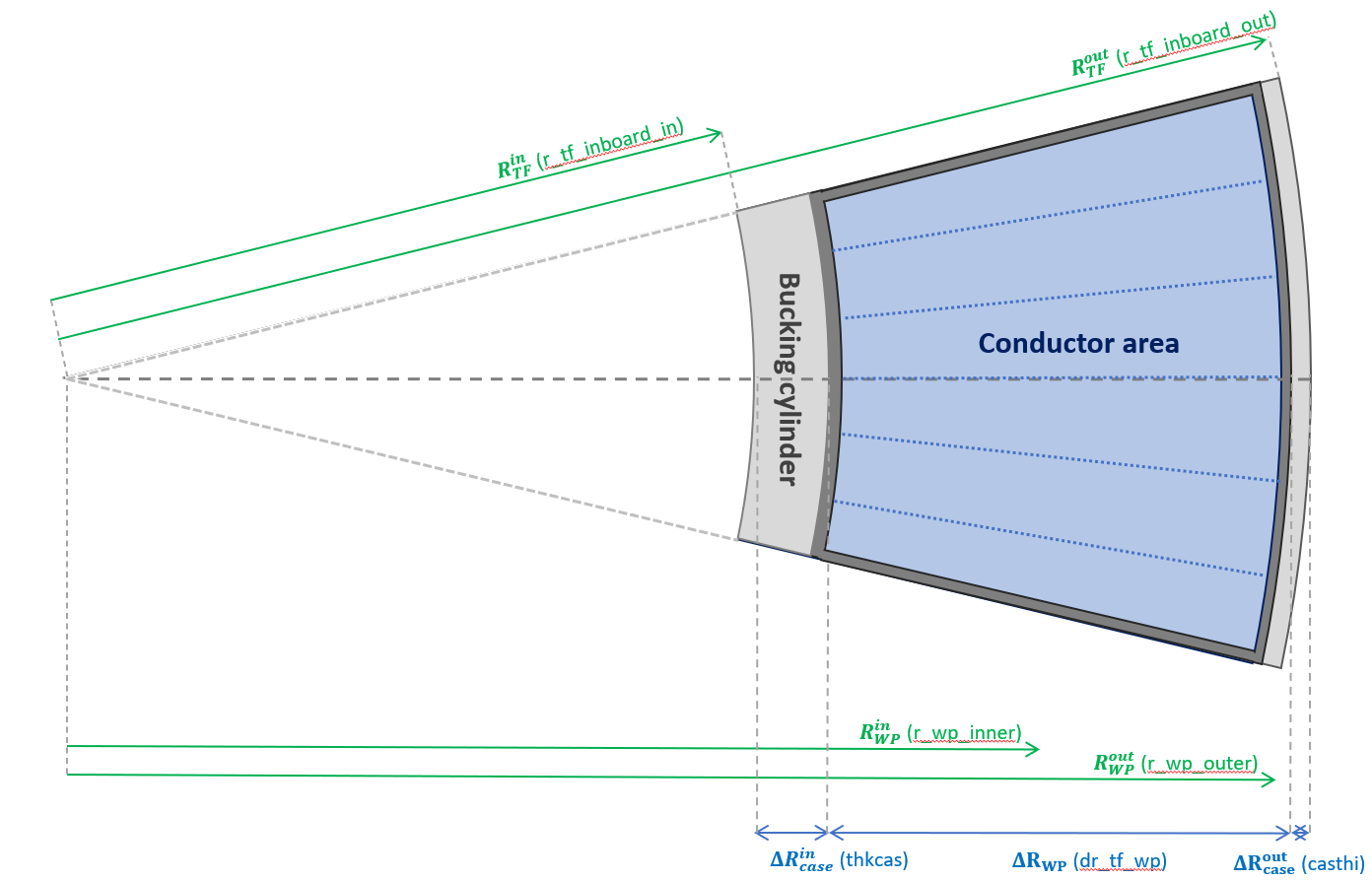
Figure 6: Resistive TF coil inboard leg structure at mid-plane. The disjoint steel case (no lateral case) are shown in light grey. The ground insulation wrapping the turns is shown in grey and the conductor region containing the turns in light blue. The dotted blue illustrate the location of the 6 coils turn.
The conductor layer is made of N_\mathrm{turn} turns per coil, set by the n_tf_turn
user input. The entire coil is wrapped with ground insulation of thickness tinstf
. Inside the ground insulation, each conductor ("turn") is wrapped in a turn insulation, thickness thicndut
. The coolant occupies using a fraction of the mid-plane cross-section given by fcoolcp
(iteration variable 23).
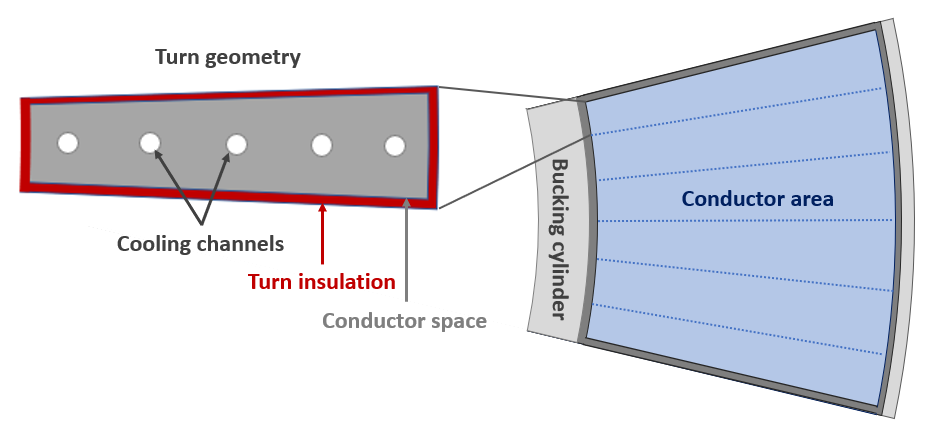
Figure 7: Schematic view of a single TF coil cross-section with four resistive turns. The positions of the cooling channels are not specified in PROCESS - only the area occupied by coolant and the channel diameters.
TF coil shape
Coil shape
Two shapes can be selected using the i_tf_shape
integer switch:
D-shape (
i_tf_shape = 1
): simplified D-shape parametrization defined in the (R,Z) plane by a straight section and four elliptical arcs. The corresponding shape is not exactly the constant tension Princeton D but, but it is not so critical as the shape is mostly used to provide the coil circumference and illustration purposes in the current version of the PROCESS code. This shape is considered by default for conventional aspect ratio tokamaks (itart = 0
).Picture frame
i_tf_shape = 2
: rectangular shape, allowing space for an eventual super-X divertor. However this design can only be used for at low aspect ratio, characterized by low vertical forces on the TF outboard section. This shape is considered by default for low aspect ratios tokamaks (itart = 1
).
Resistive coils can benefit in having a larger outboard conductor area than the inboard one, to reduce resistive heating without increasing the plasma major radius or increasing its aspect ratio. For this reason, thicker outboard can be set using the tfootfi user input defined as the ratio between ouboard and inboard TF coil legs. The possibility of having different coil thicknesses is only available for resistive coils and tfootfi would have no effect if superconducting coils are selected (i_tf_sup = 1 ).
Resistive centre-post
In a spherical tokamak the inboard legs of a resistive TF coil are known collectively as the "centre-post" (CP).
As the resistive heating depends on the magnet cross-section (in the plan perpendicular to the current direction), heating can be substantially reduced by flaring the central section of the TF coils. The corresponding shape is illustrated in the right hand side of Figure 8. The radius of the inboard leg then increases away from the midlane as shown. This design is used by default for spherical tokamaks (itart = 1).
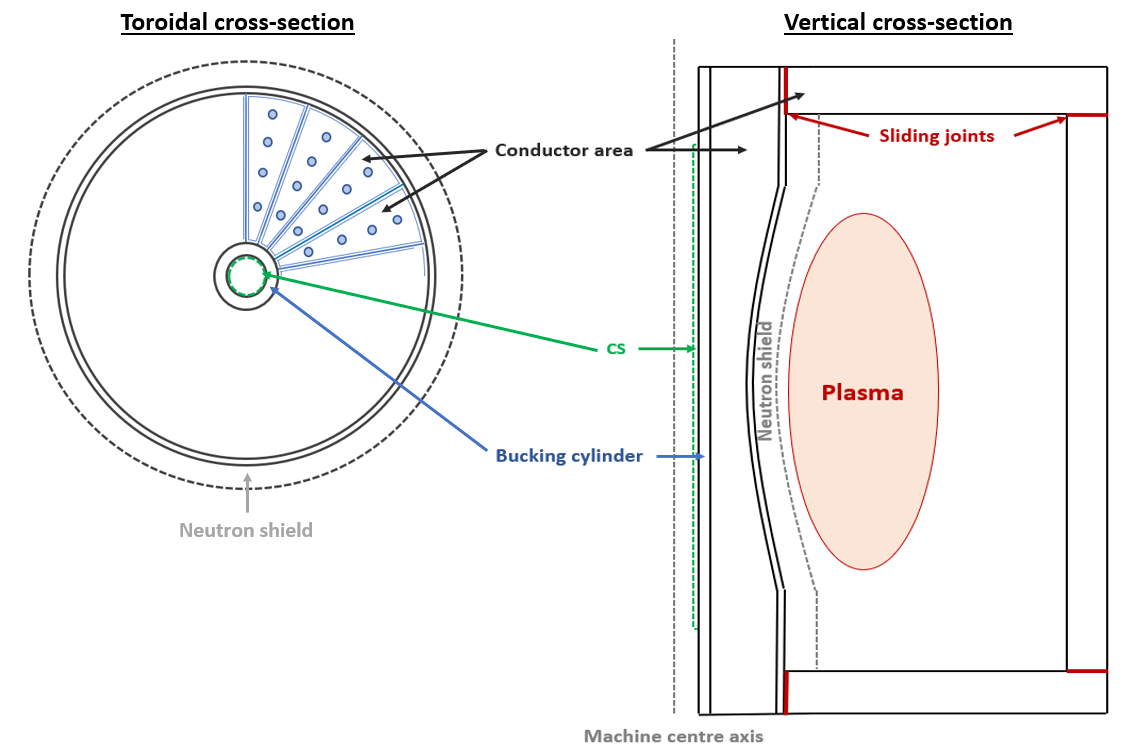
Figure 8: Mid-plane toroidal (left) and vertical (right) cross-section of a magnet using the itart == 1 geometry option. The toroidal cross-section (left) shows the presence of vaulted turn geometry with a bucking cylinder (that is not present by default for copper magnets) with insulation and cooling. The vertical cross-section (right) shows the presence of 4 sliding joints for remote maintenance purposes.
The radius of the top and bottom of the inboard leg r_cp_top
(iteration variable 174) can be set in three
different ways:
Calculated (
i_r_cp_top = 0
, default): , the top CP radius is calculated from the positions of the X-points. This option generally leads to a relatively large degree of flare.User input (
i_r_cp_top = 1
): the user sets the value ofr_cp_top
, or selects it as an iteration variable (174). Ifr_cp_top
is less than 1.01R_\mathrm{TF}^\mathrm{mid} (TF inboard mid-plane outer radius), the TF top radius is set to1.01*r_tf_inboard_out
with an error warning. Ifr_cp_top
is too large, causing the centre-post to interfere with the X-point, an error message is generated.Mid/top TF radius ratio (
i_r_cp_top = 2
):r_cp_top
is set as a ratio of the inboard mid-plane radius to the input parameterf_r_cp
, defined as \frac{ R_\mathrm{TF}^\mathrm{top} }{R_\mathrm{TF}^\mathrm{out}} . Ifr_cp_top
is too large, causing the centre-post to interfere with the X-point, an error message is generated. This option allows the shape of the centre-post to remain constant when varying the machine size.
The resistive heating, cooling requirement and material masses are calculated taking the flaring into account, parametrized with an arc. The cross-sectional area of the coolant channels is uniform throughout the centre-post, making the coolant fraction smaller at the top where less resistive heating is expected due to the larger conductor section.
TF coil joins
Another aspect of the TF coil design is the presence of demountable joints. Having demountable joints can ease the maintenance strategy by allowing to remove the inboard section of the coil vertically without moving the outboard section of the Tokamak. Moreover, if the joints allows some longitudinal and toroidal movements (sliding joints), they can also ease the TF coils structural design by significantly reducing the inboard mid-plane vertical tension. Some other advantages not captured by process of sliding joins is the reduction of out-of-plane stresses generated from PF coils fields of the TF corners. Finally, although the increase of resistive power dissipation is took into account in PROCESS, the technical feasibility of sliding joints with superconducting magnets is not addressed. The joint option can by selected by following switch:
No TF joints (
i_cp_joints = 0
, SC magnets default): this corresponds to a conservative DEMO/ITER like strategy making the coil more reliable at the cost of a more complex remote maintenance strategy.Sliding joints (
i_cp_joints = 1
, resistive magnet default): the joints is made of Feldmetal connectors allowing longitudinal sliding and toroidal torsion. Such joints allows to decouple the inboard TF coil vertical tension from the outer legs ones (effect captured in PROCESS) and cancel the out-of-plane (OOP) shear stress at the joints (effect not captured in PROCESS as OOP stress is not calculated). The joint resistive heating is also calculated and more specific design can be set by tuning the joints surfacic resistivity (rho_tf_joints
), the number of joints per coil (n_tf_joints
), the number of contact per joints (n_tf_joints_contact
) and the thickness of the joint contact (th_joint_contact
). It is possible to use sliding joints with SC coils in PROCESS, but it is not advised to do so except if the user has a very specific design in mind.
TF stress modelling
The PROCESS TF coil module only considers the inboard mid-plane stress constraint. Although it is the most stringent design constraint for the machine build, out-of-plane stress, local bending stresses due to the coil shaping, ripple and inter-coil structure effects remains to be evaluated after a PROCESS run. Inboard mid-plane stress limits can be introduced using the following constraints equations:
Conducting layer stress limit (
icc = 32
): stress limit on the conductor layer on the material take the most of stress that supports. For superconducting TF coils, the stress limit is applied on the steel case jacket/conduit while for resistive coil, the stress limit is applied on the conductor itself. Set the maximum stress using the variablesig_tf_wp_max
. This constraint can also be used with a stellarator.Centring support structure stress limit (
icc = 31
): stress limit on the coil centering support structures. For superconducting coils, this stress limit is applied on the nose case (machine center direction) while for resistive coil this stress limit is applied on a cylindrical bucking cylinder. Set the maximum stress using the variablesig_tf_case_max
. This constraint can not be used with a stellarator.
Vertical tension
No sliding joints case
The interaction between the TF coil field with the horizontal component of its current induces an identical and opposite vertical force \( F_\mathrm{z}\) on the upper and lower sections of the TF coils. If axisymmetry is assumed, this force only depends on the coil current \( \left( \frac{I_\mathrm{TF}^\mathrm{tot}}{N_\mathrm{TF}} \right) \) and its radial build. If we parametrize the conductor layer radial build with its in/outboard (\(R_\mathrm{in}\)/\(R_\mathrm{out}\) ) radii and its thickness (\(\Delta R_\mathrm{cond} \)), the vertical force is given by:
with \(B_\mathrm{T}\) and \(R_\mathrm{maj}\) the plasma center toroidal field and major radius, respectively. This force is distributed between inboard \( \left( T_\mathrm{z}^\mathrm{in}\right)\) and outboard \(\left(T_\mathrm{z} ^\mathrm{out}\right)\) legs. The resulting tensions are in general not equals as they depends on coil shape. This asymmetry is parametrized PROCESS buy the following user input f_vforce_inboard \(\left(f_{F_\mathrm{z}} ^\mathrm{in}\right)\) defined as:
with \(T_\mathrm{z}^\mathrm{in}\) the vertical tension acting on the inboard leg of a TF coil. The f_vforce_inboard default value (0.5) corresponds to the special case of a perfect Princeton-D. On the other hand a picture frame coil can show larger asymmetries with f_vforce_inboard values around 0.65.
Sliding joint case
The presence of sliding joints allows to decouple the vertical tension generated by the outboard legs horizontal current from inboard coil section. If the joints are placed just after the TF coil central section, significant inboard tension reduction can be achieved (the inboard section takes 10-20% of the total vertical force depending on the configurations). The same method as the no sliding joints case is used to estimate the vertical tension with the only difference being that the force integral is stopped at the joint location \(\left( R_\mathrm{joint}\right)\) instead of the outboard leg. The inboard vertical tension is then given by:
with \(R_\mathrm{in}\) and \(\Delta R_\mathrm{cond} \) the inboard mid-plane plasma facing side conductor radius and its inboard thickness.
Inboard mid-plane stress
The inboard mid-plane stress is calculated using a simplified cylindrical geometry. This geometry assumption applies perfectly for the resistive coil geometry but is less adapted to the SC coil more complex geometry, that mixes a discontinuous WP-case nose interface with a continuous sidewall-nose case interface depending (depending on the toroidal angle). Thus even if the PROCESS TF SC coil stress model provide acceptable (within 4-10% error margins) stress distributions for global machine design, it is advised to finalize the stress analysis with FEA models that captures the stress variations in the toroidal direction and its associated maximum stresses. Two models can be used to calculate inboard mid-plane normal stresses radial distributions. They both support an arbitrary number of different material layers and mainly differs in the way the vertical tension is introduced:
Plane stress (
i_tf_stress_model = 1
, default): the calculations are made under the plane stress assumption. Plane strain model applies for thin layer in the vertical direction and is there fore not applicable to this configuration in theory. The radial and toroidal stress calculations are made assuming no vertical tension. A constant vertical stress is then estimated a posteriori by dividing the inboard vertical tension by the support sutructure area to obtain the 3 normal stress necessary to for the TRESCA yield stress estimate as described in [1]. Although using un-adapted model hypothesis this model is still used by default as it has been validated on FEA analysis and benchmarked with the MADMAX CEA code on DEMO designs.Generalized plane strain (
i_tf_stress_model = 0,2
): the calculations are made using the generalized plane strain hypothesis that applies for tall cylinders with external external force applied at the end (vertical tension). This is the correct assumption for inboard mid-plane stress calculations that allows to derive the vertical stress distribution coherently [2]. This formulation has been developed for transverse orthotropic materials (isotropic in the \left(r, \theta\right) plane with different properties in the vertical direction). This allows to applies different Poisson's ratio, one for the \left(r, \theta\right) plane to z and another for the radial to toroidal direction. Although more coherent and complete this model is not yet used by default as more FEA validations are needed.i_tf_stress_model = 0
is the older model, which is O(n^3) in the number of layers and fails if there is a solid bore.i_tf_stress_model = 2
is the newr model, which is O(n) and accepts a solid bore, but is otherwise identical to the older modeli_tf_stress_model = 0
.
These two models can use any number of material layers with different Young modulus and Poisson's ratios for each layers (two pairs of Young modulus and Poisson's ratio are used for the generalized plane strain model). As the conductor layer of a TF coil is relatively complex, smeared properties are used to set the Young modulus, as described in the next section.
Stress layer definition
Defining the stress model layers is straightforward for resistive as the inboard coils and the model shares the same axi-symmetry (see Figure 6 ). However the SC coils inboard geometry shown in Figure 4 is more complex as the presence of lateral case breaks the axi-symmetry and the rectangular nature of the winding pack breaks the cylindrical geometry of the stress layers. Therefore, several adjustments must be made to properly define the stress model parametrization. First, as the model does not allow to take the lateral to plasma side case connection into account (axi-symmetry), the plasma side case effect is taken into account by reducing the effective vertical tension in the calculation assuming a constant vertical strain (generalized plane strain) by the following factor :
with \( A_\mathrm{steel}^{eff} \) the effective steel cross-section area defined as the total steel TF cross section \(A_\mathrm{steel}^{tot}\) minus the front casing one. For free standing coils, only two layers are therefore considered for the stress calculations TF coils (Figure 9):
Structural support layer: made of the steel case nose section. No e. m. body forces are present in this layer, therefore so the stress variations are only driven by geometrical effects (constant vertical stress)
Conductor layers: made of the winding packs and the lateral casings. Two levels of property smearing is performed for this layer, the WP-lateral case smearing and the internal WP smearing from the turn structure. This section contains the e.m. body forces driving a vertical stress radial dependency though Poisson's ratio effects.
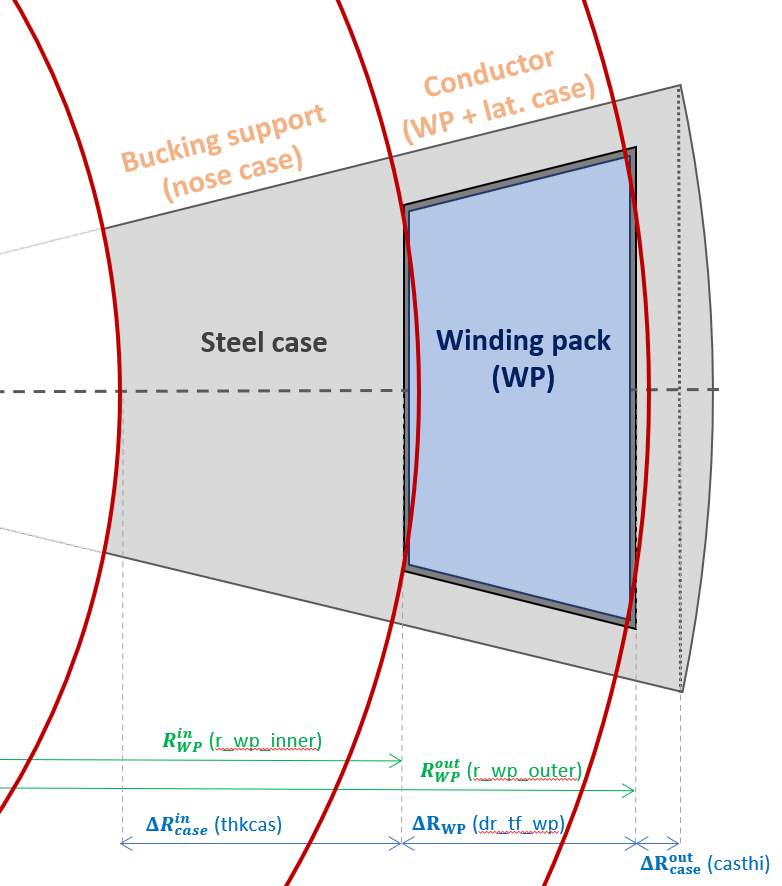
Figure 9: Positioning of the layers used in the stress calculations delimited by the red lines. The corresponding radii are defined keeping the nose and plasma side casing area constant to get consistent vertical stress calculations.
Due to the squared WP geometry, its inner/outer radius can take different values depending on the considered toroidal angle. To bypass this difficulty, the WP stress layer radii (\( R_\mathrm{WP,\ eff}^\mathrm{in/out}\)) has been defined is such a way that the nose casing and the plasma side area remain the same between the geometrical calculation and the cylindrical ones with [3]. As the property smearing is based on area fractions in the vertical direction this definition allows consistent vertical tension calculations. These \(R_\mathrm{WP,\ eff}^\mathrm{in}\) and \(R_\mathrm{WP,\ eff}^\mathrm{out}\) radii are given by:
with \(R_\mathrm{WP}^\mathrm{in/out}\) the inner or outer middle-coil WP radius used to parametrize the coil geometry (see Figure 1) and \(\theta_\mathrm{TF} = \frac{\pi}{N_\mathrm{TF}}\) the half radial extent of the TF coil inboard leg.
Structural properties smearing
Resistive coil conductor smearing
The resistive TF coil properties are only smeared in the vertical direction to take the effect of the cross section taken by the cooling and the, with the corresponding effective young modulus \(\bar{E_\mathrm{z}}\)
with \(E_\mathrm{ins}\)/\(E_\mathrm{cond}\) the insulation layer/ conductor material Young modulus and \(f_\mathrm{ins}\)/\(f_\mathrm{cool}\) the insulation/conductor cooling mid-plane cross-section area fractions. \(f_\mathrm{ins}\) is calculated from the insulation layers thicknesses and number of turns while \(f_\mathrm{cool}\) is a defined by the user with fcoolcp, defined with the conductor area after the insulation area subtracted. Even though the presence of insulation layer tends lower the Young modulus in the toroidal direction, no property smearing is done for now for resistive coils for now.
Superconducting coil winding pack smearing
The transverse and the vertical WP smeared properties are calculated separately. The WP smeared Young modulus in the vertical direction \(\bar{E}_\mathrm{z}^\mathrm{WP}\) is calculated assuming constant vertical strain (generalized plane strain or parallel case), and is give by:
with \(A^\mathrm{steel}_\mathrm{WP\ eff}\) and \(A^\mathrm{ins}_\mathrm{WP}\) being the area taken by the WP steel turn jackets plus the sidewall case area and the WP total insulation area, respectively. The WP transverse properties are calculated decomposing the turn geometry in series (constant strain), as illustrated in Figure 10.
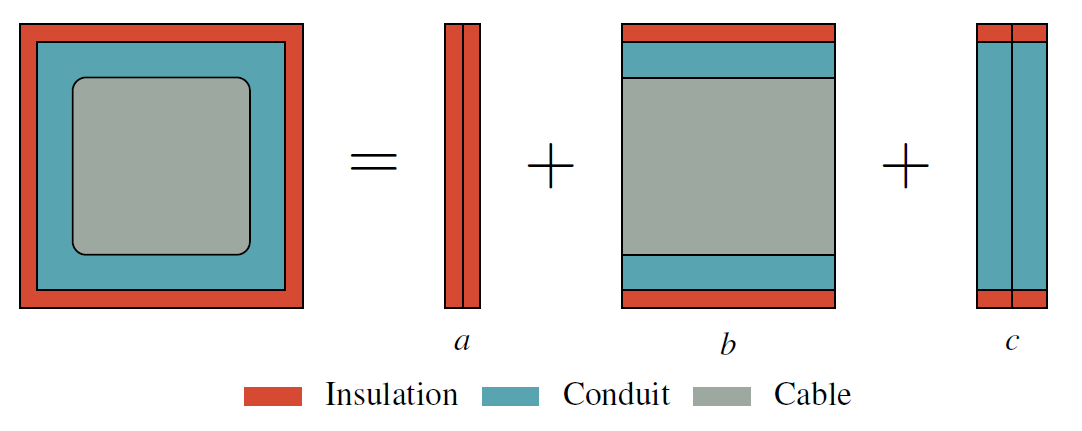
Figure 10: turn structure decomposition used to estimate the average winding pack average Young modulus. The decomposition is made considering a vertical stress component, corresponding to a parallel decomposition (constant strain).
As the steel conduit is much stiffer the force is approximated to go only on the \(c\) section, lowering the young by ratio between the total and the steel conduit case thickness. This approximation is wrong if the insulation's or the conductor cable Young modulus is at the same order of magnitude as the steel support's one. The \(c\) section properties are then calculated using the series case assumption (constant stress). The final WP effective young modulus is then given by
with \( t_\mathrm{ins} \), \( t_\mathrm{turn} \) and \( t_\mathrm{cond} \) the insulation, turn and steel conduit structures thicknesses. For CICC cables the vertical Young's modulus is generally about 2-3 times larger than the transverse. It is expected as the vertical smearing is based on steel area and the transverse one steel thickness ratios, with the support structure being round the cable, the area ratio is naturally more favorable. Finally, to properly take the effect on the lateral casing on the WP layer properties, an additional series smearing is performed, using the average lateral casing thickness for the smearing. The effective Young modulus for the stress calculation is therefore given by:
with \(\left< t_\mathrm{side\ case} \right>\) and \(\left< t_\mathrm{side\ case } \right>\) the average thickness in the toroidal direction of the sidewall case and the winding pack, respectively. If the integer turn option is used (i_tf_turns_integer = 1), the cases are not always squared. The smearing procedure will therefore produce a different young modulus in the radial and the toroidal direction. However, a study using a similar stress model, but with fully orthotropic material (different radial and toroidal Young modulus) [3], has shown that the radial direction Young's modulus value has almost no effect on the stress distribution ITER like magnets. For this reason the toroidal direction Young modulus on the toroidal direction is used as the WP transverse young modulus.
Stress unsmearing
The raw stress distributions calculated with the smeared properties cannot be used directly for the conductor structural constraints. The stress distribution must be corrected to get the stress on the actual support structures. The un-smeared support structure stress on the vertical direction \(\sigma_ \mathrm{zz}\) is obtained simply by:
A stress unsmearing is also necessary on the transverse direction for SC coils. Two unsmearing transverse factors are defined (lateral and toroidal), that will differ if the integer turn option is selected (non squared turns selected with i_tf_turns_integer = 1).
Inboard TF coil support
Several centering forces support options structures are proposed in PROCESS,
selected with the i_tf_bucking
integer switch.
No support (
i_tf_bucking = 0
): the TF coil is only made of a conducting layer. This is the default option for copper magnets (i_tf_sup = 0
). However, as the superconducting magnets winding pack is surrounded by a closed steel case, this option is incompatible with superconducting coils (i_tf_sup = 1
).Free standing TF bucking (
i_tf_bucking == 1
): the conductor is supported by a dedicated centering support and is not in contact with the CS coil. This support is nown as a bucking cylinder for resistive magnets, and is referred to as the 'nose' of the case for superconducting magnets. This is the default option for aluminium (i_tf_sup = 2
) and superconducting magnets (i_tf_sup = 1
).Bucked and wedged (
i_tf_bucking == 2,3
): the TF coil uses the CS coil as centering forces structural support. This design allows to substantially reduce the thickness of the TF coil individual suport structure if a large CS coil is present. As the CS coil current generates a beneficial CS radial outward forces, the most critical instant for structural support is the moment when no current flows in the CS coil. The CS coil is therefore represented as an additionnal stress layer withe.m.
no body forces. The layer strctural properties are defined using using similar smearing/ unsmeating procedure as the TF coil, as detailed in issue [4]. The maximum between the CS stress from the this model and the on calculated in thepfcoil
module is taken as the CS coil stress limit (constraint 72). A fast version, neglecting the interface layer properties is implemented (i_tf_bucking == 2
). And a more complete one, taking explicitly the Kapton interface into account in the stress calcualtions (i_tf_bucking == 3
) is also implemented. Before using this design option, the user must know two major potential issues not captured by PROCESS. The first is the fatigue introduced by the CS on the TF coil. The second is the nature of the CS-TF coil interface that has to allow vertical slinding at cryogenic temperatures, as the CS vertical size reduces when energized and the TF coil vertical tension makes TF grow taller with current flowing in it. The CS and the TF coil are therefore strain insulated, therefore all the vertical tension is taken by the TF coil structures.
It is also possible to fill the CS coil bore with structural material to further support the TF centering forces. Although not currently implemented in PROCESS, to technical issues prevents simulating its structural effects. Please contact the PROCESS team if you wish to consider this option in your design and you are sure to understand the increase in complexity such design requires.
Stress limits
The maximum of the stress distributions after unsmearing, is used to compute the TRESCA yield stress, defined as:
The transverse stresses (\(\sigma_\mathrm{rr}\) and \(\sigma_\mathrm{\theta\theta}\)) are negative and the vertical streess (\(\sigma_\mathrm{zz}\)) positive. As the toroidal stress is generally larger than the toroidal one, the \(\left| \sigma_\mathrm{\theta\theta} - \sigma_\mathrm{zz} \right|\) term is expected to drive the yield stress value. The associated constraint equations are the 31, 32 and the 72 (if i_tf_bucking == 2 or 3). The value of the Von-Mises yeild stress is also shown in the output for information.
TF coil ripple
Because of the finite number of TF coils used in a tokamak (18 for ITER and 16 for DEMO), the axisymmetry is effectively broken. Therefore, in addition to the radial dependency, the toroidal field also varies as a function of the toroidal angle and the vertical position. This effect is known as ripple. Electromagnetic ripple impacts TF coil design in two ways:
Plasma ripple: The toroidal filed variation on the low field side generates some instabilities that degrades the plasma confinement. Moreover, some significant fast particles losses can be present if the field variation becomes too large between coils, threatening the divertor and first wall integrity.
On coil ripple: If the lateral case is separating the conductor region (winding pack), the genuine magnetic field at the inboard superconducting conductor is larger than the value obtained using the axisymmetric assumption.
Plasma ripple
The maximum plasma ripple is defined in PROCESS with the user input ripmax
as:
with \( B_\mathrm{min}\) and \( B_\mathrm{max}\) minimum field (between coils) and the maximum field (on coil toroidal direction) respectively, measured at the mid-plane plasma outer limit (separatrix). PROCESS plasma ripple is estimated using a parametric Bio-Savart calculation fitted using the UKAEA free boundary MHD code FIESTA. The shape (Princeton-D) used for these MHD model is shown in the left section of Figure 11.
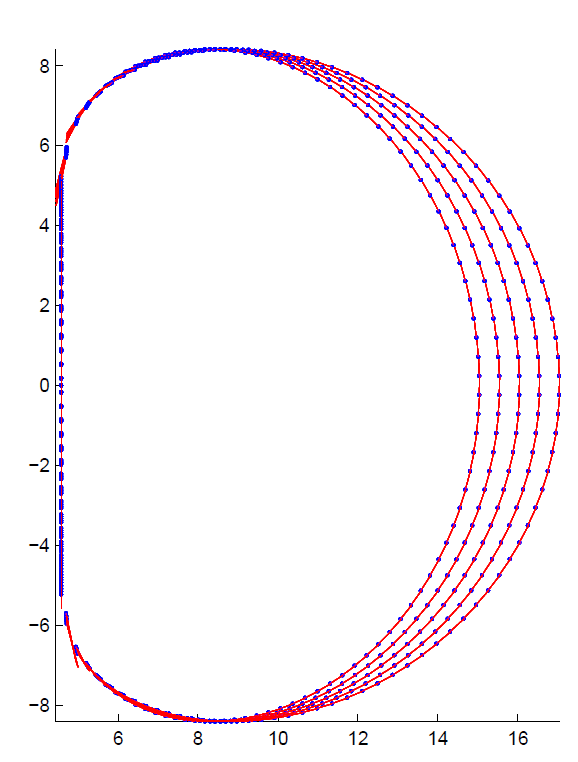
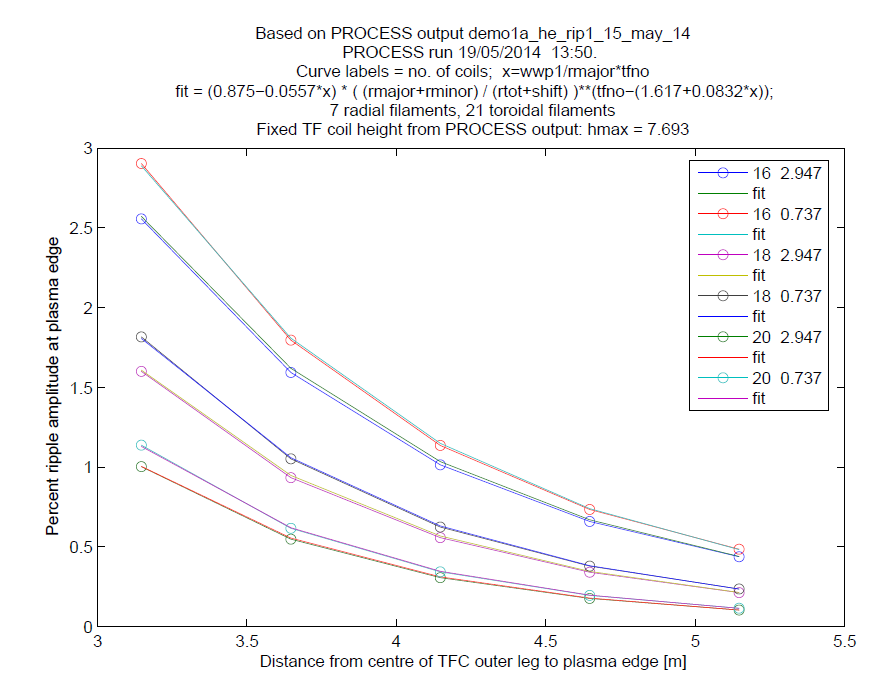
Figure 11 : The left graph shows the filament shape used in the FIESTA ripple calculations. The current loops are made straight section (red lines) connecting vertices (blue dots) following the coil shape. The right plot shows the ripple calculated by FIESTA (lines with open circles) compared to the fit values (lines without circles) for different number of coils (16, 18 and 20) and lateral winding pack to TF size ratio (\(x = 0.737\) and \(x = 2.947\)) as a function of the outer leg winding centre position.
The results of the ripple fit is shown on the right section of Figure 11 and its analytical expression given by:
with \(x\) the lateral thickness of the winding pack normalized to the coil dimensions defined as:
with \(\Delta R_\mathrm{tWP}^\mathrm{out}\) the plasma side WP thickness defined in the Figures 1 and 3, \(N_\mathrm{TF}\) the number of coils and \(R_\mathrm{maj}\) the plasma centre radius. \(y\) is the plasma outer mid-plane separatrix to outboard TF leg mid-plane radius ratio:
with \(a_\mathrm{min}\) the plasma minor radius and \(R_\mathrm{outboard\ TF} ^\mathrm{mid}\) the TF winding pack outboard leg midplane radius at its centre. The scaling fitting range is provided by:
Number of coils: N_\mathrm{TF} \in \{16, 18, 20\} .
Winding pack size ratio: x \in [0.737-2.95]
separatrix to TF ratio: y \in [0.7-0.8]
To prevent intolerable fast particles losses and plasma instabilities, \(\delta\) must be limited to a few percent, approximatively \( \delta \in [0.5-1]\) . If intolerable, the plasma ripple can be reduced with many different techniques, for example the TF coil shape, stabilisation coils can be added, more coils can be used or the coil outboard radius can be increased. All these design modifications affects the coil system design, for example ripple shape optimisation should be done without generating too much bending stress due to the un-adapted curvature radius, and adding coils must not prevent remote maintenance. To keep the design procedure as simple as possible in PROCESS, unacceptable ripple is reduced by simply moving the TF coil leg to a larger radius. The outboard ripple is directly obtained reverting the ripple fit to provide \(R_\mathrm{outboard\ WP}^\mathrm{mid}\) as a function of the ripple. The minimal \(R_\mathrm{outboard\ WP}^\mathrm{mid}\) is technically obtained by increasing the gap between the vacuum vessel and the coil (gapsto).
The currently implemented plasma ripple evaluation assumes a Princeton-D shape and is therefore not valid anymore if very different shapes are considered, with picture frame coils, for example, different models should be considered/implemented in PROCESS.
On coil ripple
The ratio of TF coil magnetic field increase with respect to the axisymmetric formula has been defined as :
with \(B_\mathrm{rip}\) being the maximum field measured at the middle of the plasma facing sides of the winding pack and \(B_\mathrm{nom}\) the nominal maximum field obtained with the axisymmetric formula (see section TF coils current). The same FIESTA runs have been used to estimate the on-coil ripple. This peaking factor has been fitted separately for 16, 18 and 20 coils using the following formula:
with the \(A_n\) the fitted coefficients and \(t\) the relative winding pack lateral thickness defined as:
with \(\Delta R_\mathrm{tWP}^\mathrm{out}\) defined in Figure 1 and 3 and \( \Delta R_\mathrm{tWP}^\mathrm{out\ max} \) the same value calculated without sidewall case as illustrated in Figure 12.
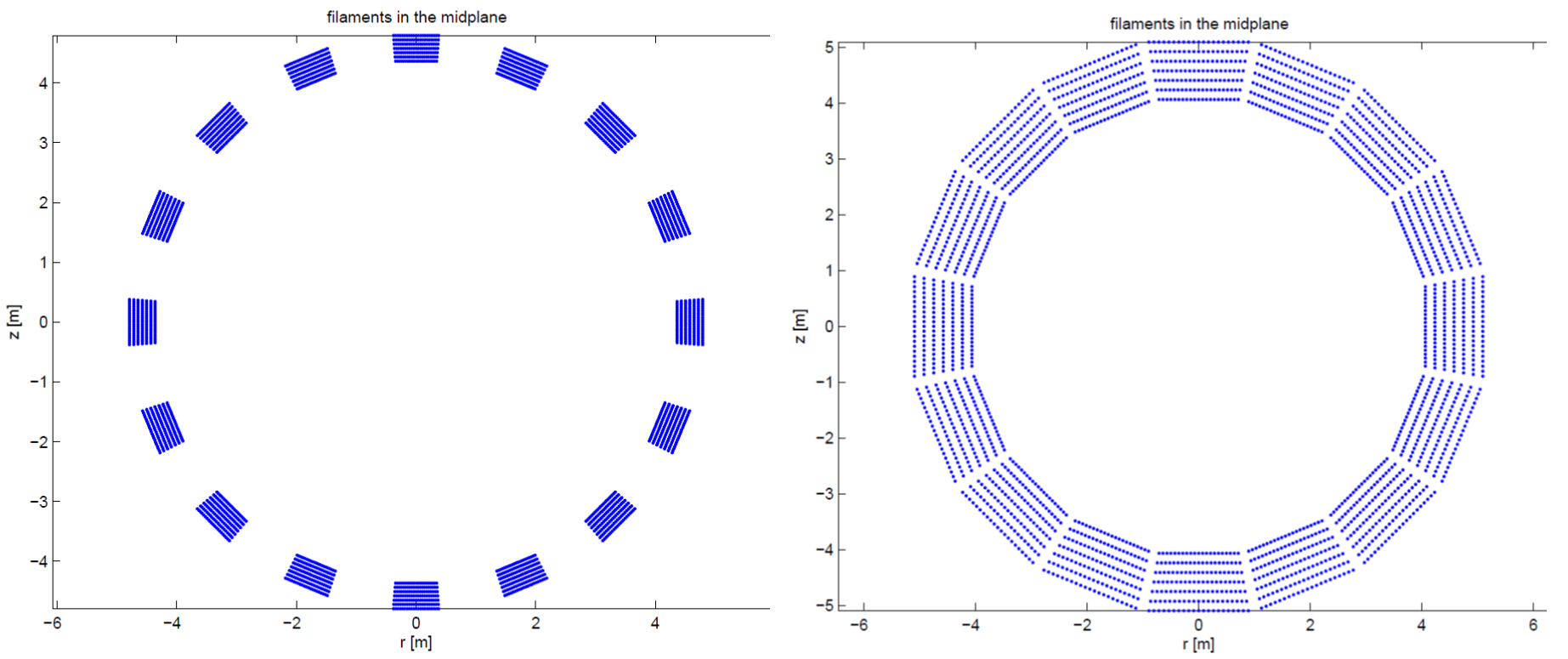
Figure 12: Inboard midplane cross section showing the filaments used for the on-coil ripple calculations with FIESTA with 16 coils. A radial and toroidal winding pack thickness of 0.5 m and 0.8 m for the left graph, while a radial and toroidal thickness of 1.2 m and 1.9 m, respectively, is used in the right figure. The right graph provides a visual illustration of the case where the parameter \(t\) is close to unity.
And the relative winding pack radial thickness \(z\) given by
The three fits (for 16, 18 and 20 coils) are valid for:
relative toroidal thickness: t\in[0.35-0.99]
relative radial thickness: z\in[0.2-0.7]
Number of TF coils: Individual fits has been made for 16, 18 and 20. For any other number of coils, the FIESTA calculations are not used and a default ripple increase of 9% is taken ( f_\mathrm{rip}^\mathrm{coil} = 1.09). This default value is also used for 17 and 19 coils.
Figure 13 shows a contour plot of the on-coil ripple peaking factor as a function of the winding pack sizing parameters for 16 coil.
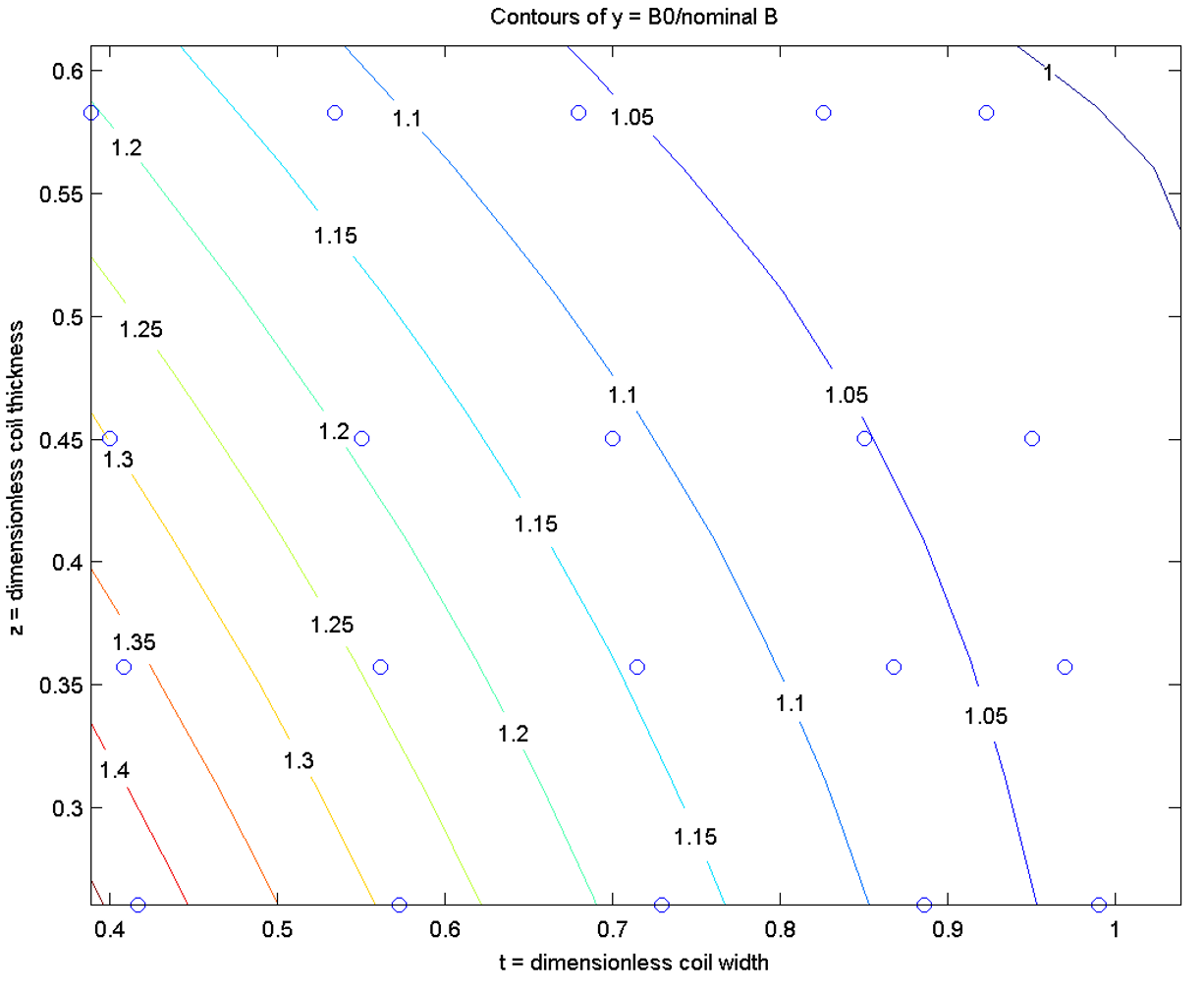
Figure 13: Contour plots of the on-coil peaking factor \(f_\mathrm{rip} ^\mathrm{coil}\) obtained with FIESTA and used in the PROCESS scaling for 16 coils. The horizontal and vertical axis corresponds to the relative transverse \(t\) and radial thickness \(z\), respectively.
These ripple calculations are out of the spherical tokamak design range, having generally fewer coils (between 10 and 14) and more radially thick winding packs. It is also worth mentionning that the the ripple must be evaluated layer-by-layer for graded coil designs, to get the genuine B field of each layer used to quatify the SC cross-section area per layer. Finally, resistive coils do not suffer from on-coil ripple as there is no radial case is present.
TF coil stored energy
The stored magnetic energy is calculated.
Critical current density for the superconductor
The minimum conductor cross-section is derived from the critical current density for the superconductor in the operating magnetic field and temperature, and is enforced using constraint 33.
Switch i_tf_sc_mat
specifies which superconducting material is to be used:
i_tf_sc_mat == 1
-- Nb_3Sn superconductor, ITER critical surface parameterization5, standard critical valuesi_tf_sc_mat == 2
-- Bi-2212 high temperature superconductori_tf_sc_mat == 3
-- NbTi superconductori_tf_sc_mat == 4
-- Nb_3Sn superconductor, ITER critical surface parameterization5, user-defined critical parametersi_tf_sc_mat == 5
-- WST Nb_3Sn parameterizationi_tf_sc_mat == 6
-- REBCO HTS tape in CroCo strandi_tf_sc_mat == 7
-- Durham Ginzburg-Landau critical surface model for Nb-Tii_tf_sc_mat == 8
-- Durham Ginzburg-Landau critical surface model for REBCOi_tf_sc_mat == 9
-- Hazelton experimental data combined with Zhai conceptual model for REBCO
The fraction of copper present in the superconducting filaments is given by fcutfsu
(iteration variable number 59).
For i_tf_sc_mat = 2
, a technology adjustment factor fhts
may be used to modify
the critical current density fit for the Bi-2212 superconductor, to describe the
level of technology assumed (i.e. to account for stress, fatigue, radiation,
AC losses, joints or manufacturing variations). The default value for fhts
is
0.5 (a value of 1.0 would be very optimistic).
For i_tf_sc_mat = 4
, important superconductor properties may be input as follows:
- Upper critical field at zero temperature and strain: bcritsc
,
- Critical temperature at zero field and strain: tcritsc
.
The toroidal field falls off at a rate 1/R, with the peak value occurring at the outer edge of the inboard portion of the TF coil winding pack (radius rbmax
).
Three constraints are relevant to the operating current density J_{\mbox{op}} in the TF coils.
- Criticial current (
constraint 33
): J_{\mbox{op}} must not exceed the critical value J_{\mbox{crit}}. Iteration variable 50 must be active (fiooic
). The current density margin can be set using the upper bound offiooic
:
-
Constraint 35
-- To ensure that J_{\mbox{op}} does not exceed the current density protection limit, constraint equation no. 35 should be turned on with iteration variable 53 (fjprot
). -
Temperature margin (
constraint 36
) -- The critical current density J_{\mbox{crit}} falls with the temperature of the superconductor. The temperature margin \Delta T is the difference between the current sharing temperature (at which J_{\mbox{crit}} would be equal to J_{\mbox{op}}) and the operating temperature. The minimum allowed \Delta T can be set usingtmargmin
together with constraint equation 36 and iteration variable 54 (ftmargtf
). Note that if the temperature margin is positive, J_{\mbox{op}} is guaranteed to be lower than \jcrit, and so constraints 33 and 36 need not both be turned on. It is recommended that only one of these two constraints is activated.
Resistive heating
To be done. Please contact the PROCESS team if you need more informations.
Code structure
The TF coil structure is illustrated by the box diagram in Figure 14.
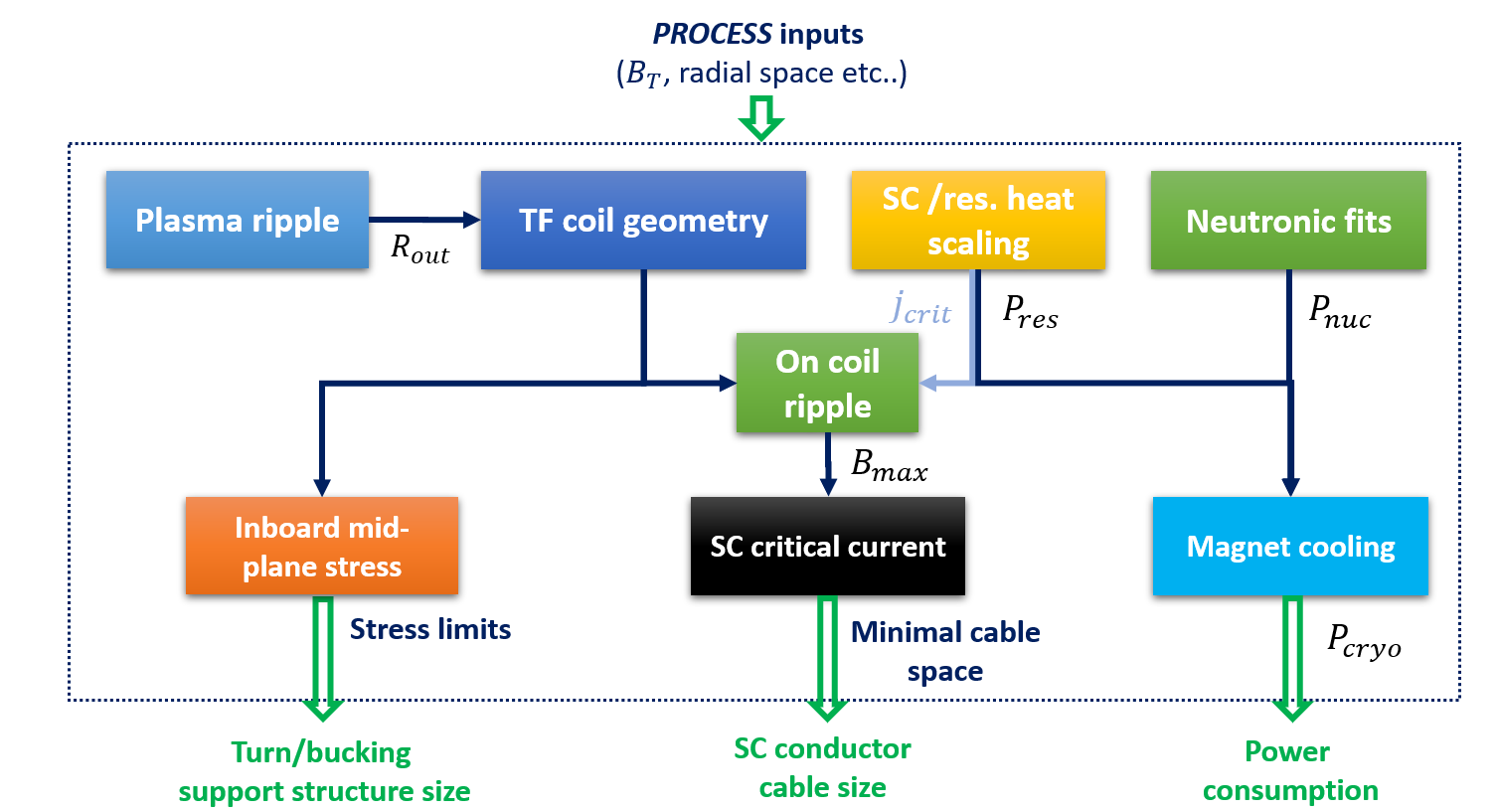
Figure 14: Box diagram illustrating the TF coil codes structure in PROCESS. The neutronic/plasma ripple/magnet cooling boxes are effectively placed in other modules, but should be effectively contained in an eventual standalone version of the module.
More technically, models are coded in the sctfcoil
subroutine, structured in
the following order:
ripple_amplitude
: Plasma ripple. Subroutine effectively contained inmachine_build.f90
tf_global_geometry
: In/outboard leg areas at mid-lanetf_current
: Calculate the TF coil currentssc_tf_internal_geom
/res_tf_internal_geom
: Set the exact superconducting/resistive magnets inboard mid-plane geometry, including the Turn geometry.coilhap
: Define the vertical TF coil shapetf_res_heating
: Estimate the TF coil resistive heating (not used for SC magnets)tf_field_and_force
: Estimate the inboard/outboard vertical tensionstfcind
: Estimate the TF coil inductancetf_coil_area_and_masses
: Estimate the mass of the different coil materialspeak_tf_with_ripple
: Estimate the ripple peak field correction.stresscl
: Estimate the inboard mid-plane stress distributions.
Another subroutine, tfspcall
is called outside stfcoil
to estimate to check on the TF superconducting properties.
TF coil parameter summary table
General parameters
Parameter | description | Default |
---|---|---|
n_tf |
Number of TF coils | 16 |
i_tf_sup |
Swich selecting the conductor technology: - 0 : Water cooled copper (GLIDCOP) - 1 : Superconducting TF magnets - 2 : Helium cooled Aluminium magnets |
1 |
i_tf_sc_mat |
Swich for superconducting material 1 : Nb_3Sn superconductor, ITER critical surface parameterization1, standard critical values 2 : Bi-2212 high temperature superconductor 3 : NbTi superconductor 4 : Nb_3Sn superconductor, ITER critical surface parameterization1, user-defined critical parameters 5 : WST Nb_3Sn parameterization 6 : REBCO HTS tape in CroCo strand 7 : Durham Ginzburg-Landau critical surface model for Nb-Ti 8 : Durham Ginzburg-Landau critical surface model for REBCO 9 : Hazelton experimental data combined with Zhai conceptual model for REBCO |
1 |
Mid-plane geometry parameters
Parameter | description | Iteration variable | Default | Unit |
---|---|---|---|---|
tf_in_cs |
TF coil inboard leg radial placement switch. - 0 : Outside of central solenoid - 1 : Inside of central solenoid |
- | 0 | - |
tfcth |
TF coil maximum radial size calculated if dr_tf_wp is used as iteration variable |
ixc = 13 | No default | m |
tfootfi |
Outboard/inboard TF coil thickness ratio | - | 1 | - |
dr_tf_wp |
Winding pack radial thickness calculated if tfcth is used as iteration variable. Include the ground insulation and the insertion gap. |
ixc = 140 | No default | m |
thkcas |
Nose/inner case radial thickness | ixc = 57 | 0.3 | m |
casths |
Minimal sidewall casing thickness | - | - | m |
casths_fraction |
Minimal sidewall casing thickness as a fraction of the TF coil toroidal thickness. Overwites the casths input value |
- | 0.03 | - |
casthi |
Minimal plasma side casing thickness | - | - | m |
casthi_fraction |
Minimal plasma side casing thickness as a fraction of the TF thickness (tfcth ). Overwites the casthi input value |
- | 0.05 | - |
i_tf_case_geom |
Plasma side casing geometry option: - 0 : rounder front casing (ITER) - 1 : Straight casing |
- | 0 | - |
i_tf_wp_geom |
Winding pack geometry option: - 0 : rectangular - 1 : double rectangle - 2 : trapezoidal |
- | Integer turn : 0 otherwise : 1 |
- |
tinstf |
WP ground insulation thickness | - | 0.018 | m |
tfinsgap |
WP insertion gap thickness | - | 0.01 | m |
Turn parameters
Parameter | description | Iteration variable | Default | Unit |
---|---|---|---|---|
i_tf_turns_integer |
Switch activating the integer turn parametrization - 0 : Integer number of turns - 1 : non integer number of turn |
- | 0 | - |
n_layer |
Number of turns in the radial direction (i_tf_turns_integer = 1 only) |
- | 20 | - |
n_pancake |
Number of turns in the toroidal direction (i_tf_turns_integer = 1 only) |
- | 10 | - |
t_turn_tf |
TF turn squared size | - | No default | m |
t_cable_tf |
TF cable diameter size | - | No default | m |
f_t_turn_tf |
f-value for TF turn squared size constraint (icc = 86) | 175 | 1. | m |
t_turn_tf_max |
Maximum turn squared size for constraint (icc = 86) | - | 0.05 | m |
cpttf |
Current per turn Overwitten if t_turn_tf is set by the user |
ixc = 60 | 70.10^3 | A |
thicndut |
Turn insulation layer thickness | - | 0.8.10^{-3} | m |
thwcndut |
Steekl jacket/conduit thickness | 58 | 8.10^{-3} | m |
dhecoil |
Helium cooling channel diameter | - | 5.10^{-3} | m |
vftf |
Cable void fraction | - | 0.4 | - |
fcutfsu |
Copper cable fraction defined with the cable area minus the void and cooling channel area |
ixc = 59 | 0.69 | - |
Vertical shape
Parameter | description | Iteration variable | Default | Unit |
---|---|---|---|---|
itart |
Switch for tapered inboard TF section 0 : conventional inboard leg 1 : Tapered inboard leg (centrepost, CP) |
- | 0 | - |
i_tf_shape |
Switch selecting the TF coil shape 1 : D-shape approximation 2 : Rectangular (picture frame) shape |
- | 1 : if itart = 0 2 : if itart = 1 |
- |
r_cp_top |
CP TF coil top/bottom radius | ixc = 174 | No default | m |
f_r_cp |
CP TF top/mid-plane outer radius fraction | - | 1.4 | - |
i_r_cp_top |
Switch selecting the r_cp_top parametrization 0 : r_cp_top calculated using the X-point location 1 : Set by user 2 : Set with f_r_cp |
- | 0 | - |
TF coil joints
Parameter | description | Iteration variable | Default | Unit |
---|---|---|---|---|
i_cp_joints |
Switch selecting the TF coil demoutable joints strategy 0 : No demountable joints 1 : MAST like sliding joints |
- | 0 : if itart = 0 1 : if itart = 1 |
- |
n_tf_joints |
Number of joints per coils | - | 4 | - |
n_tf_joints_contact |
Number of contacts per joints | - | 6 | - |
rho_tf_joints |
Joint surfacic resistivity | - | 2.5.10^{-10} | \Omega.m |
th_joint_contact |
Joint contact thickness | - | 0.03 | m |
TF coil inboard mid-plane stress
Parameter | description | Iteration variable | Default | Unit |
---|---|---|---|---|
f_vforce_inboard |
Fraction of the vertical force supported by the inboard leg | - | 0.5 | - |
i_tf_stress_model |
Switch to select the inboard mid-plane stress model 1 : Plane stress 0,2 : Generalized plane stress |
- | 0 | - |
i_tf_bucking |
Switch to select the bucking strategy 0 : No bucking structure 1 : TF bucking structure 2 : TF bucked on CS coil 3 : TF bucked on CS coil (CS-TF layer included in the stress calc.) |
- | 0 : if i_tf_coil \= 1 1 : if i_tf_coil = 1 |
- |
TF coil python utilities
The plot_stress_tf.py utility provides a summary of the stress calculations providing by plotting the radial distributions of:
Radial displacement used to calculated the strain/stress distribtions. No toroidal displacement is assumed on the vertical direction due to up/down symmetry and no toriodal diplacement is present as axysymmetry is assumed in the stress model
Smeared normal strains: in the radial, toroidal and vertical directions. By definition the vertical strain distribution is constant in the generalized plane strain formulation. Continuous toroidal strain and discontinuouns radial strain is expected between the different layers.
Smeared normal stress: in the radial, toroidal and vertical directions. Vertical stress is expected to vary in the condictor layer but to remain constant in each other layers (no body forces). Continuous radial stress is expected as the layers are assumed to be in contact while discontinous toroidal stress is expexted between layer if the toroilal young modulus are different.
Structure normal stress: in the three directions. These corresponds to the stress after unsearing. The associated Von-Mises and TRESCA yield are also shown. The maximum TRESCA stress is used to set the limit on the TF coil structures.
Please note that only a fraction of the plots will be performed if the plane stress option is chosen (this is the default stress option). The full set of plots is however performed if the generalized plane strain option chosen.
TF coil fast discharge : stress in vacuum vessel
In a TF coil fast discharge a large poloidal current is induced in the vessel. See Vacuum Vessel.
References
(Updated 13/4/23)
-
"PROCESS": A systems code for fusion power plants - Part 2: Engineering M. Kovari, F. Fox, C. Harrington, R. Kembleton, P. Knight, H. Lux, J. Morris Fusion Engineering and Design 104 (2016) 9-20 ↩↩
-
Derivation_of_multilayer_generalized_plain_strain.docx in PROCESS issue 991 ↩
-
J_c(B,T,\epsilon) Parameterizations for the ITER Nb_3Sn Production', ITER Document 2MMF7J (2008), \texttt{https://user.iter.org/?uid=2MMF7J\&action=get_document} ↩↩